Stal jest jednym z fundamentów współczesnej cywilizacji – spotykamy ją w budynkach, mostach, pojazdach i niezliczonych przedmiotach codziennego użytku. Ale jak właściwie powstaje stal i różnorodne wyroby stalowe, takie jak pręty zbrojeniowe, blachy, rury czy profile? W tym artykule prześledzimy pełen cykl produkcji stali – od wydobycia surowców, przez wytop żelaza i stali w hutach, ich rafinację i walcowanie, aż po uformowanie konkretnych produktów stalowych. Unikając nadmiaru technicznego żargonu, krok po kroku zobaczymy, jak ze skały i złomu powstają stalowe serca naszych konstrukcji.
Wielki piec: wytop surówki żelaza
Pierwszym etapem produkcji stali (w hutach zintegrowanych) jest otrzymanie płynnego żelaza z rudy – dokonuje się tego w urządzeniu zwanym wielkim piecem. Wielki piec to wysoki (nawet 30-metrowy) szybowy piec, do którego od góry wsypuje się warstwami spieki rudy żelaza, koks i topniki (wapień). Od dołu natomiast wdmuchuje się gorące powietrze (często wzbogacone tlenem), które powoduje spalanie koksu. W temperaturze około 1500°C żelazo ulega stopieniu i gromadzi się na dnie pieca jako surówka – płynne żelazo zawierające do 4% węgla oraz domieszki innych pierwiastków.
Niżej topi się także topnik z zanieczyszczeniami, tworząc ciekły żużel, który unosi się na powierzchni cięższej surówki. Otrzymana surówka żelaza to jednak jeszcze nie stal – zawiera zbyt dużo węgla i zanieczyszczeń, jest krucha i nie nadaje się do użycia konstrukcyjnego. Musi trafić do stalowni, gdzie w specjalnych piecach zostanie przerobiona na stal.
Stalownia: przekształcanie żelaza w stal
Surówkę z wielkiego pieca oraz dodatek złomu stalowego przetapia się na stal w stalowni. Odbywa się to najczęściej jedną z dwóch metod: konwertorową lub elektryczną. W procesie konwertorowym, powszechnym w wielkich hutach, płynna surówka jest wlewana do olbrzymiego naczynia zwanego konwertorem. Następnie przez metal przetłacza się czysty tlen. Tlen gwałtownie utlenia nadmiar węgla oraz innych domieszek (krzemu, fosforu, siarki) zawartych w surówce. Reakcje te są bardzo burzliwe – metal wrze, wyrzucając snopy iskier i płomieni – ale dzięki nim zawartość węgla spada do pożądanego poziomu (poniżej ~2%). W efekcie w ciągu kilkunastu minut surówka zamienia się w płynną stal o odpowiednim składzie chemicznym.
Alternatywnie, w metodzie elektrycznej, używanej często w mniejszych stalowniach i przy recyklingu złomu, stal produkuje się w piecu elektrycznym łukowym (EAF). Taki piec to ogromna „miska” stalowa wyłożona materiałem ogniotrwałym, do której ładuje się złom stalowy. Z góry opuszczane są elektrody węglowe, między którymi przeskakuje silny łuk elektryczny. Łuk ten rozgrzewa złom do temperatury topnienia (ponad 1500°C). Topienie w piecu elektrycznym trwa zwykle około godziny – po tym czasie uzyskuje się kilkadziesiąt ton ciekłej stali. Proces ten jest bardziej elastyczny, pozwala też łatwiej wytwarzać stale specjalne (np. stopowe, ze ściśle kontrolowanymi dodatkami stopowymi), ponieważ można precyzyjniej dozować składniki i korzystać z czystego złomu.
Rafinacja stali i ciągłe odlewanie
Niezależnie od metody wytopu, świeżo otrzymana płynna stal wymaga jeszcze dopracowania składu i nadania jej formy stałej do dalszej obróbki. Rafinacja stali odbywa się często poza głównym piecem. Stal może zostać przelana do kadzi wyposażonych w system grzewczy i umożliwiających przedmuch gazów obojętnych (argon). W takich kadziach usuwa się resztki zanieczyszczeń (np. siarki, wodoru) i dokładnie reguluje zawartość domieszek. Dodawane są też pierwiastki stopowe (np. chrom, nikiel, mangan) jeśli chcemy uzyskać stal o specjalnych właściwościach, np. nierdzewną czy sprężynową.
Kolejnym krokiem jest odlewanie stali do form, aby zastygła w użytecznej postaci półwyrobów. Dawniej stal lało się do dużych kokil, gdzie krzepła jako bloki (tzw. wlewy), ale dziś prawie wszędzie stosuje się wydajniejsze odlewanie ciągłe. W procesie ciągłego odlewania ciekła stal spływa z kadzi przez wąski wylew do miedzianej, chłodzonej wodą formy o prostokątnym przekroju.
Wlew ciągły jest stopniowo, wysuwany z maszyny odlewniczej i schładzany – tworzy on długi, stężały pas stali, który jest następnie cięty nożycami tlenowymi lub mechanicznymi na poręczne długości (kilka do kilkunastu metrów). Tak powstają półfabrykaty stalowe gotowe do dalszej obróbki plastycznej.
Walcowanie i formowanie stali
Aby z półwyrobów otrzymać gotowe produkty – pręty, blachy, szyny, profile – stal musi zostać poddana obróbce plastycznej. Najbardziej powszechną metodą jest walcowanie na gorąco. Polega ono na przepuszczaniu rozgrzanego kawałka stali (np. kęsa lub slabu) między obracającymi się walcami, które niczym wałkowanie ciasta spłaszczają lub wydłużają metal do pożądanego kształtu i wymiaru. Walcowanie zwykle odbywa się w temperaturach rzędu 1000–1200°C, gdy stal jest miękka i podatna na kształtowanie. Grube, prostokątne slaby walcuje się stopniowo na coraz cieńsze blachy; kwadratowe kęsy – na długie pręty, druty czy kształtowniki. Proces odbywa się na liniach walcowniczych składających się z wielu klatek walcujących ustawionych jedna za drugą – stalowy półwyrób przelatuje przez nie, stając się coraz cieńszy i dłuższy.
Innym sposobem plastycznego kształtowania stali jest kucie, stosowane zwłaszcza do masywnych elementów lub nadawania specjalnych kształtów. Kucie może być ręczne (kowal uderza młotem w rozgrzany metal na kowadle) lub maszynowe – w potężnych kuźniarkach i prasach. Prasa kuźnicza wywiera ogromny nacisk, który powoduje uplastycznienie i uformowanie stali w matrycach. Dzięki kuciu otrzymujemy np. osie kolejowe, wały turbin czy formy do odkuwek – elementy o wysokiej wytrzymałości, bo podczas kucia wewnętrzna struktura stali zostaje zagęszczona.
Cięcie i wykrawanie to kolejne operacje – ostudzony już metal można ciąć mechanicznie nożycami gilotynowymi, piłami, a w przypadku blach także wykrojnikami lub palnikiem tlenowym czy laserem. Finalnie, niektóre wyroby poddawane są gięciu lub innym operacjom wykańczającym (np. gwintowaniu końców prętów, wierceniu otworów w profilach).
Po walcowaniu na gorąco wiele produktów poddaje się jeszcze obróbce wykańczającej. Na przykład cienkie blachy po ostygnięciu mogą być dalej walcowane na zimno, co poprawia ich gładkość i własności wytrzymałościowe, albo pokrywane powłokami (np. cynkowaniem, by stworzyć blachę odporną na korozję). Pręty mogą być cięte na zadane długości i prostowane, a druty – nawijane w kręgi. Gotowe półprodukty stalowe stają się bazą do wytwarzania konkretnych wyrobów użytkowych.
Wyroby stalowe i ich produkcja
Otrzymaną stal można formować w różne typy wyrobów, zależnie od przeznaczenia. Skupmy się na czterech głównych grupach: pręty zbrojeniowe, blachy (i taśmy), rury stalowe oraz profile stalowe. Choć wszystkie powstają z tego samego materiału, różnice w ich kształtach i zastosowaniach sprawiają, że linie produkcyjne wyglądają nieco inaczej.
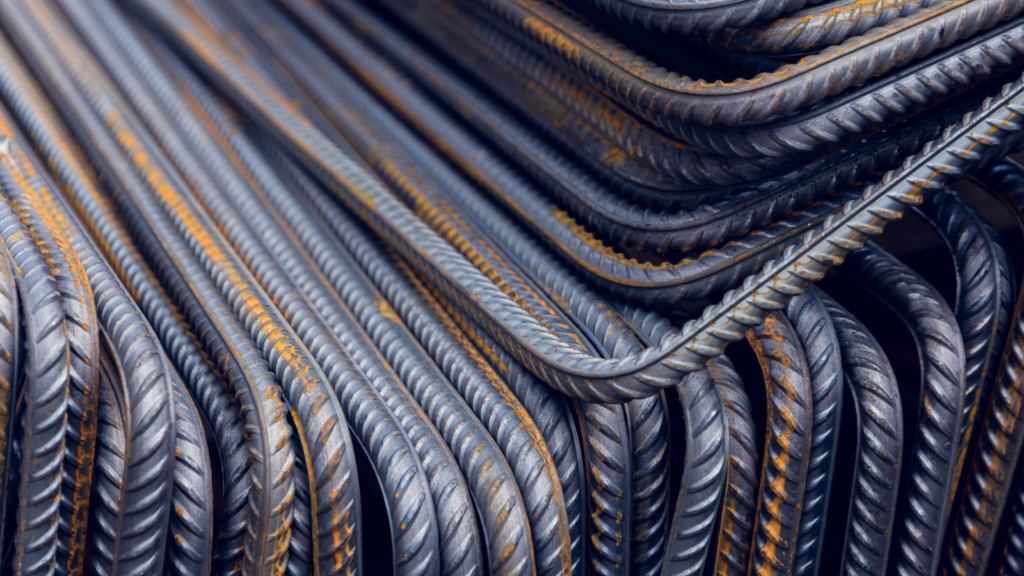
Pręty zbrojeniowe
Pręty zbrojeniowe to charakterystyczne stalowe pręty z wyżłobionymi żeberkami na powierzchni, używane do wzmacniania betonu w konstrukcjach żelbetowych. Produkuje się je masowo metodą walcowania na gorąco. Proces zwykle zaczyna się od nagrzania do czerwoności stalowych kęsów o przekroju kwadratowym (np. 12×12 cm) do temperatury ok. 1100°C. Taki rozgrzany kęs jest wielokrotnie przepuszczany przez ciąg walców, które posiadają wżłobienia formujące – stopniowo wyciągają one materiał, zmniejszając jego średnicę i wydłużając go, aż powstanie długi pręt o wymaganym przekroju (najczęściej od 6 do 40 mm średnicy). Ostatnie walce nadają powierzchni pręta charakterystyczne żebra (występy spiralne lub poprzeczne), dzięki którym pręt lepiej trzyma się betonu po zalaniu.
Wychodzące z walcarki rozpalone pręty są następnie chłodzone, gdzie stygną do temperatury otoczenia. Potem tnie się je na standardowe odcinki (typowo 6, 12 lub 18 metrów) i wiąże w pakiety gotowe do transportu. Walcownie zbrojeniowe pracują ciągle, wyrzucając z siebie setki ton prętów dziennie. Co ważne, do wytwarzania prętów zbrojeniowych często wykorzystuje się stal z recyklingu – wiele zbrojarni bazuje na stali ze złomu przetopionej w piecach elektrycznych, co jest bardziej ekologiczne.
Ponieważ pręty zbrojeniowe nie muszą mieć idealnie gładkiej powierzchni czy bardzo precyzyjnych wymiarów (żebra wręcz są pożądane, a drobne odchyłki nie szkodzą), ich produkcja jest stosunkowo prosta i tania. Dzięki temu zbrojenia są jednym z najtańszych wyrobów stalowych, wytwarzanym na ogromną skalę na potrzeby budownictwa.
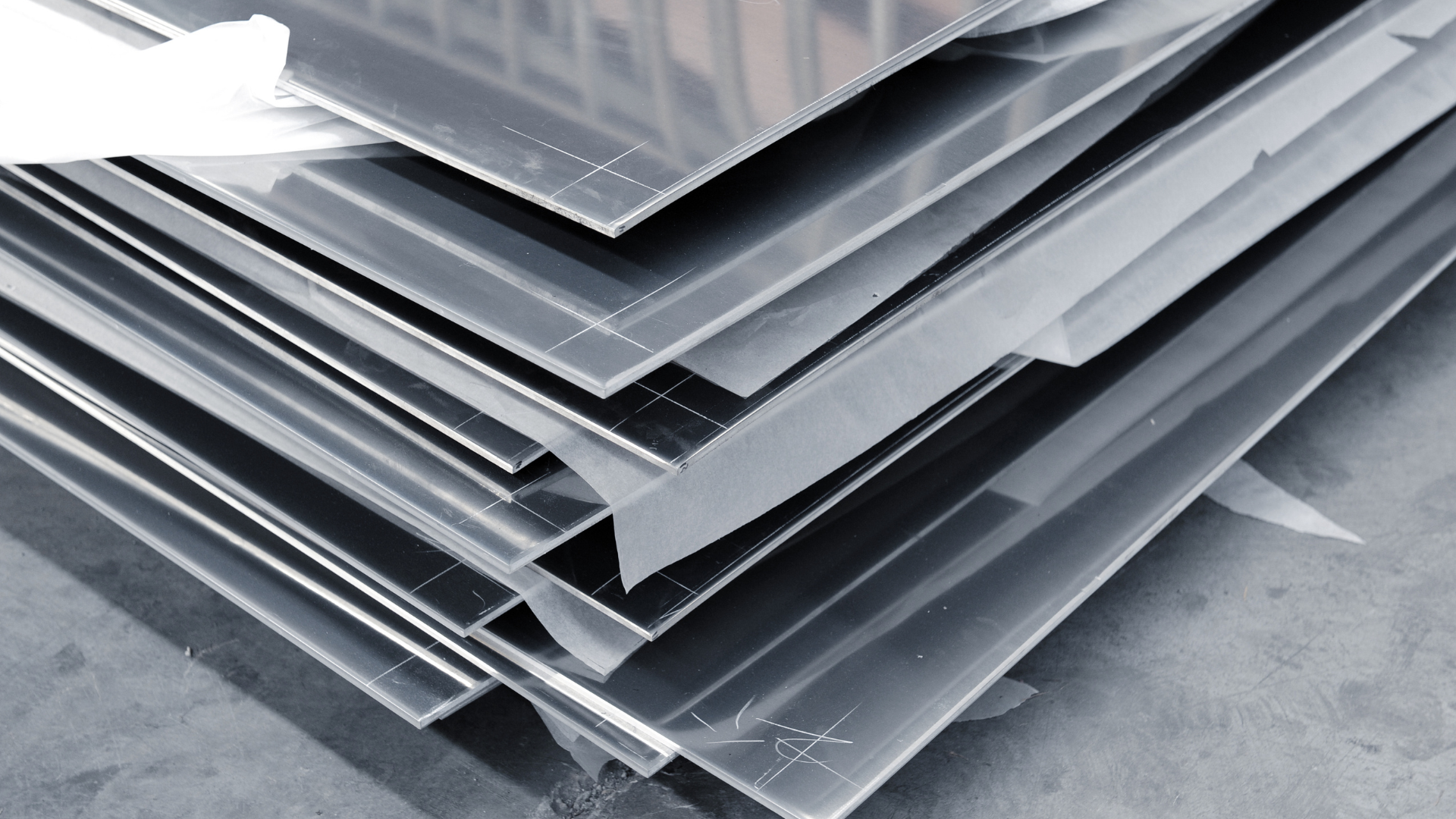
Blachy i taśmy stalowe
Blachy stalowe to płaskie arkusze metalu, używane m.in. na poszycia konstrukcji, obudowy maszyn, karoserii samochodów czy dachów budynków. Produkcja blach wymaga przekształcenia stali w formę szerokich, cienkich płatów. Odbywa się to poprzez walcowanie płaskich półwyrobów (slabów) na coraz mniejszą grubość. Taki slab jest następnie rozgrzewany do około 1200°C w piecu pokrocznym, po czym trafia do walcarki wstępnej, która zmniejsza jego grubość do kilku centymetrów. Kolejne walcarki – zespół walcarki wykańczającej – walcują materiał do finalnej grubości blachy, która może wynosić od kilku milimetrów (dla blach grubych konstrukcyjnych) do zaledwie ułamków milimetra (dla najcieńszych blach folowych, walcowanych na zimno).
Często jednak blachy wytwarza się jako ciągłą taśmę stalową nawiniętą następnie w olbrzymią rolę – taki zwój stali nazywamy kręgiem. Jest to wygodne w transporcie i dalszej obróbce (blachy zwoju rozwija się stopniowo w innych maszynach). Grubsze blachy (np. 8–20 mm) zwykle pozostają w formie arkuszy i trafiają do odbiorców jako blachy uniwersalne. Cieńsze, bywają zwijane w kręgi już po walcowaniu na gorąco. Natomiast bardzo cienkie blachy (poniżej ~3 mm) często poddaje się jeszcze walcowaniu na zimno.
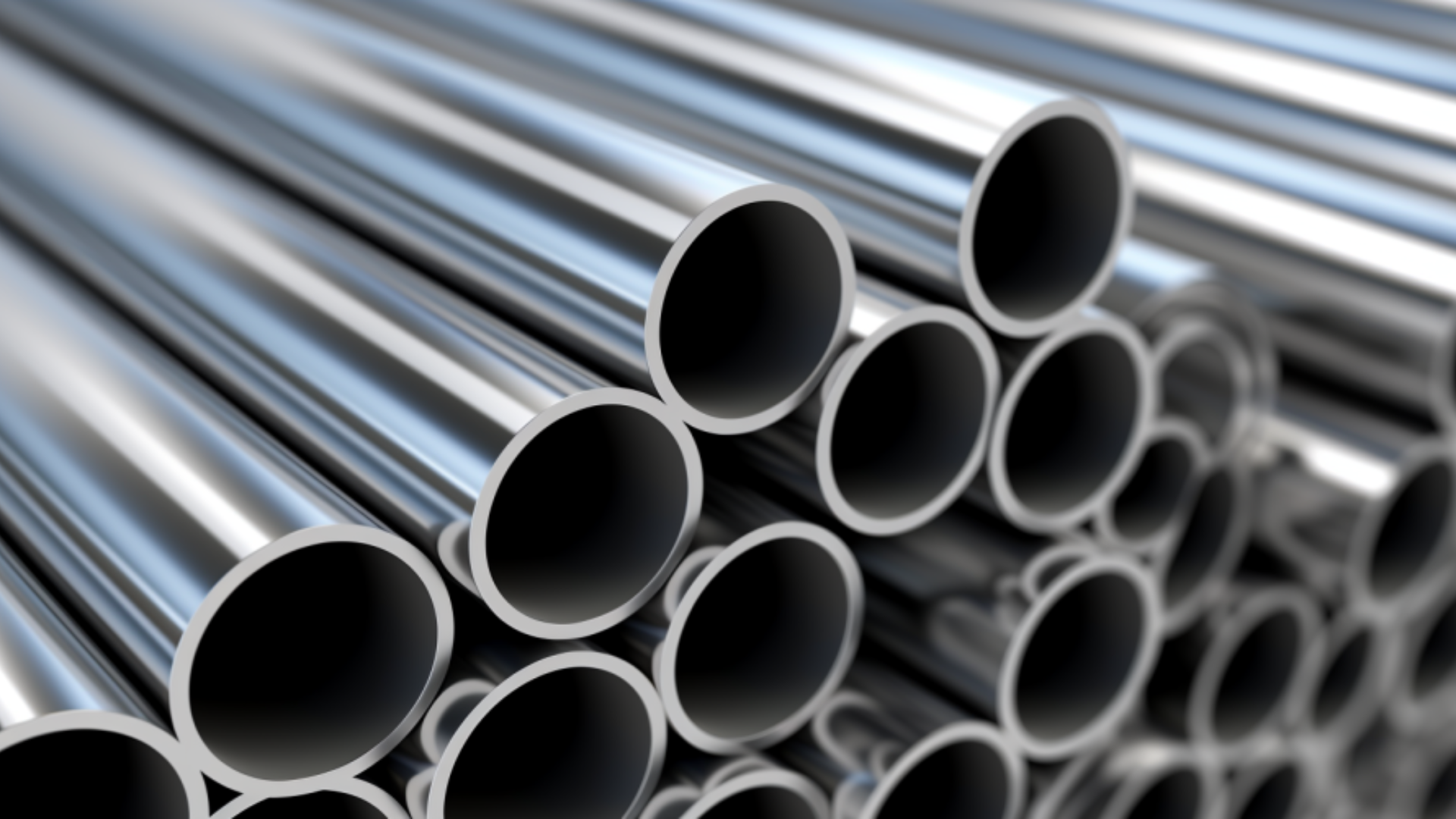
Rury stalowe
Rury to wyroby w kształcie pustego cylindra – wszechobecne w przesyle mediów (woda, gaz, ropa), konstrukcjach (rusztowania, ogrodzenia) czy częściach maszyn. Wytwarzanie rur stalowych odbywa się dwoma głównymi metodami: bez szwu (rury bezszwowe) oraz z szwem (rury spawane).
Rury bezszwowe powstają z pełnego kawałka stali, w którym wykonuje się otwór – nie mają więc linii łączenia na obwodzie. Klasyczny sposób to walcowanie pielgrzymowe: nagrzany stalowy walec jest przebijany długim kolcem (tzw. trzpieniem), który drążąc otwór tworzy z walca tuleję. Następnie tuleja ta jest poddawana obróbce przez specjalne walce, które poszerzają i wydłużają ją, formując żądaną średnicę i grubość ścianki rury. Proces odbywa się na gorąco – metal musi być rozżarzony, aby dał się tak rozciągnąć.
Bezszwowe rury charakteryzują się brakiem słabych punktów – wytrzymują duże ciśnienia i obciążenia, dlatego stosuje się je np. w przemyśle naftowym czy energetycznym (kotły, rurociągi ciśnieniowe).
Rury ze szwem natomiast powstają z płaskiej blachy lub taśmy, która jest zawijana w kształt rury, a następnie jej krawędzie są ze sobą zespawane. To bardziej ekonomiczna metoda dla rur o większych średnicach i do zastosowań, gdzie nie wymaga się ekstremalnych wytrzymałości. Przykładem są rury przewodowe do wody czy gazu, rury konstrukcyjne w halach, słupy itp. Do ich produkcji używa się długich pasów blachy odpowiedniej szerokości. Krawędzie stykające się ze sobą są następnie łączone trwałym spoinowym łączeniem. Dawniej używano spawania piecowego lub kuźniczego, dziś powszechne jest spawanie elektryczne bądź spawanie wysoką częstotliwością (HF). Powstały szew spawalniczy jest mocny, ale stanowi jednak potencjalną linię osłabienia – dlatego rury spawane stosuje się tam, gdzie mogą mieć nieco niższe parametry niż bezszwowe.
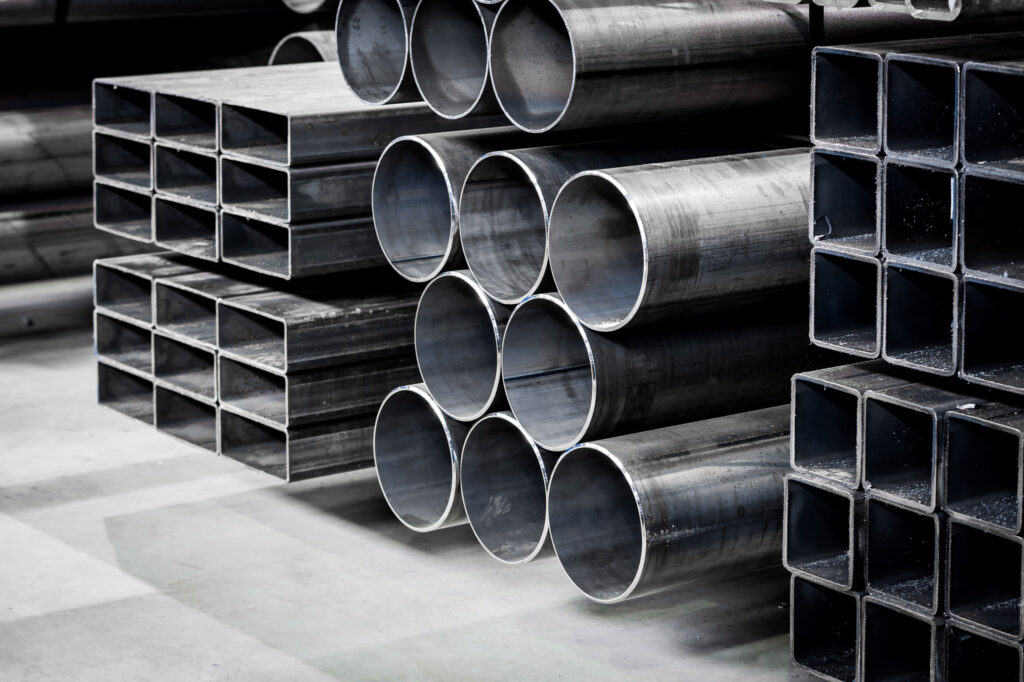
Profile stalowe
Profile stalowe (kształtowniki) to elementy o przekroju innym niż okrągły czy płaski – należą do nich np. Dwuteowniki (popularne „dwuteówki” o przekroju przypominającym literę H lub I), ceowniki (w kształcie C), kątowniki, teowniki oraz profile zamknięte kwadratowe/prostokątne.
Profile te są podstawowymi „klockami” konstrukcyjnymi w budownictwie i przemyśle – tworzy się z nich szkielety hal, mostów, maszyn. Wytwarza się je głównie przez walcowanie na gorąco w specjalnych walcowniach kształtowników. Proces jest podobny do walcowania prętów, ale walce mają wycięcia o kształcie odpowiadającym połowie przekroju profilu. Stalowy podłużny półprodukt przechodzi kolejno przez zestaw takich walców, gdzie jest zgniatany i formowany. Dla dużych kształtowników (np. dwuteowniki wysokości kilkuset milimetrów) potrzebne są potężne walcarki i kilkukrotne przejścia, a proces musi utrzymywać równomierne nagrzanie, by metal płynnie wypełnił wykroje walców.
Mniejsze profile zamknięte – takie jak kwadratowe lub prostokątne rury konstrukcyjne cienkościenne – wytwarza się często metodą podobną do rur spawanych. Startuje się od taśmy blachy, formuje ją w kształt kwadratu i spawa wzdłuż jednego boku, tworząc długą zamkniętą sekcję. Następnie przechodzi ona przez układ rolek, które dogniatają boki do kąta prostego i kalibrują wymiary. W efekcie powstają profile prostokątne o wymiarach np. 40×20 mm, 100×100 mm itd., powszechnie używane w ramach, słupkach ogrodzeń czy konstrukcjach mebli stalowych.
Profilowanie stali może odbywać się również na zimno – dotyczy to zwłaszcza cienkich elementów giętych z blachy, jak profile U i C stosowane w systemach gipsowo-kartonowych czy lekkich konstrukcjach. Wówczas stalowa taśma jest gięta w profil za pomocą ciągu rolek, bez podgrzewania. Takie wyroby mają jednak ograniczoną grubość ścianki (są cienkie, do kilku milimetrów) i służą lżejszym obciążeniom.
Podsumowanie
Jak widać, droga od surowej rudy do gotowego wyrobu stalowego jest długa i składa się z wielu etapów. Każdy z nich – od wydobycia, przez hutniczy wytop żelaza i stali, po walcowanie, kucie, cięcie i formowanie – wymaga potężnych urządzeń i precyzyjnej kontroli. Efektem tej złożonej drogi są jednak materiały o niezwykłych właściwościach: stal łączy twardość z elastycznością, jest stosunkowo tania, a do tego w pełni poddaje się recyklingowi. Dlatego stal od ponad 150 lat pozostaje kluczowym materiałem konstrukcyjnym i nic nie wskazuje na to, aby miało się to zmienić.